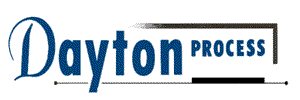
The Dayton Process
provides a safe method of fluoride-ion cleaning using a unique fluorocarbon route, which offers:
- High quality performance
- Safe operation
- Low costs
-
High applicability

Fluoride-ion cleaning
is the most effective way of removing oxides of noble metals such as aluminium and titanium from service-run components made from modern superalloys.
The thoroughly cleaned surfaces and cracks are essential for the enhanced wetting that is required to braze full both wide gaps and tight cracks.

Options:
Depending on the customer’s existing equipment and his particular requirement for the process, we offer a number of options: These range from a full turnkey package to selected hardware and technical support. As a minimum we would supply:
- A retort or retorts sized to suit the customer’s application
- Technical adjustments and specifications for the customer-supplied hardware to ensure that these meet the needs of the process
- The program details for the cleaning cycles
- Know-how transfer and training during the commissioning period and startup
The Advantages:
- Gaseous cleaning
- reaches all surfaces
- No water vapour problems
- Low temperature monomer gas reactions clean without over-etching.
- No problem of intergranular attack
The Advantages:
- Cheap, readily available, non toxic raw materials
- Generates a minimum quantity of active products, retained in an enclosed retort
- No toxic waste or raw material storage problems
- Low operating and maintenance costs
- Removal of M. CrAlY Coatings
- OEM approved
Summary
The Dayton Process offers a safe cost-effective method of fluoride-ion cleaning which is approved by Rolls-Royce and Pratt & Whitney for braze repairs and is acceptable to health/environmental authorities.
The process offers fluoride-ion cycles for different purposes. Extensions to the process for use in stripping of coatings are developed and a full technical backup service is available.